Setting a Higher Bar for Biosolids in Texas
The Trinity River Authority of Texas (TRA) is a water conservation and reclamation district that preserves clean water for a healthy environment across almost 18,000 square miles of north and central Texas. TRA operates multiple water reclamation facilities, the largest of which is the Central Regional Wastewater System (CRWS) wastewater treatment plant. CRWS serves 1.2 million people, including 20 communities in the Mid-Cities area of the Dallas metroplex, as well as the Dallas-Fort Worth International Airport. The facility has a permitted flow of 162 million gallons per day (mgd) and has historically produced lime-stabilized biosolids for land application.
Beginning in 2011, TRA commissioned a solids master plan that laid out a new course for CRWS. The master plan proposed replacing the lime-stabilization process with a more sustainable approach, one that utilizes the innovative net-zero thermal hydrolysis technology followed by digestion. Thermal hydrolysis will allow the facility to save money while providing the opportunity to recover useful resources from biosolids. CDM Smith partnered with TRA to design this upgrade for CRWS, which will make it one of the most innovative facilities in the country.
More Advanced, More Sustainable
TRA’s mission of being an innovative, adaptive leader in the water reclamation industry led the Authority to choose the thermal hydrolysis process, a pre-treatment technology that uses high-pressure steam to break down biosolids. When followed by digestion, this process can provide several options for beneficial reuse, including the ability to produce a fertilizer-grade biosolids product, the ability to compost, or to land-apply the biosolids.
“TRA’s long-term goal was to be more advanced, more sustainable, and more flexible,” says Samir Mathur, PE, CDM Smith discipline leader for water reclamation and thermal hydrolysis expert. “Transforming the way that CRWS handles biosolids meant a whole new direction for the facility and the communities it serves, and will provide multiple outlets for the facility’s biosolids.”
The reduction in biosolids volume that will be created by this project results in less truck hauling of biosolids off of the plant site, which translates into substantial cost savings. TRA expects to see an 11-year payback on the initial capital investment and $150M in savings over 30 years.
Transforming the way that CRWS handles biosolids means a whole new direction for the facility and the communities it serves.
Building on Experience
When TRA began its biosolids improvements program, thermal hydrolysis had only been implemented in one location in the U.S.—the landmark project at DC Water’s Blue Plains advanced wastewater treatment plant. To capitalize upon the success of that project and to build on the lessons learned from its implementation, TRA retained CDM Smith to design a comparable system.
“TRA’s project is the next generation of thermal hydrolysis, so we’re carrying forward the innovation elements from the DC Water project, while evolving the designs further,” says Peter Loomis, PE, CDM Smith discipline leader for biosolids. “Many aspects of design and implementation have been enhanced by our previous experience.”
For example, the CDM Smith team had learned from experience that when biosolids cooling is done in a single stage, heat loss during winter months can present challenges to controlling temperature. As a result, the CRWS cooling system was designed to operate in two stages, with the first stage cooling from ~90°C to 70°C, and the second stage blending digested biosolids and cooling further to 35° C. This adaptation will allow the CRWS facility to work more optimally and efficiently year-round.
State-of-the-Art Methods
The implementation of thermal hydrolysis is only one innovative aspect of this project. Not only will this new system create a high-quality fertilizer product, but a large volume of digester gas will be used for process boiler fuel. The facility will also be set up for addition of future combined heat and power systems driven by biogas, if desired. TRA also has the option to build additional resource recovery systems, such as struvite harvesting, in conjunction with the thermal hydrolysis system. This project sets up CRWS to implement the full suite of net-zero technologies, when and if the circumstances are beneficial for the facility.
Innovation extended to the design process. Virtual design and construction (VDC) tools were used to develop digital assets during design, which will be carried forward into operation of the systems to help them operate at peak efficiency. And, as constructability reviews found ways to improve the design, each of these improvements were built into the evolving digital model. With a single VDC model to work from, all members of the project team are working from the same guidelines, no matter what changes occur during the construction process.
By charting a new course toward resource recovery, TRA is setting a higher bar for water reclamation in Texas. The thermal hydrolysis upgrades to CRWS are expected to be completed and commissioned by 2020.
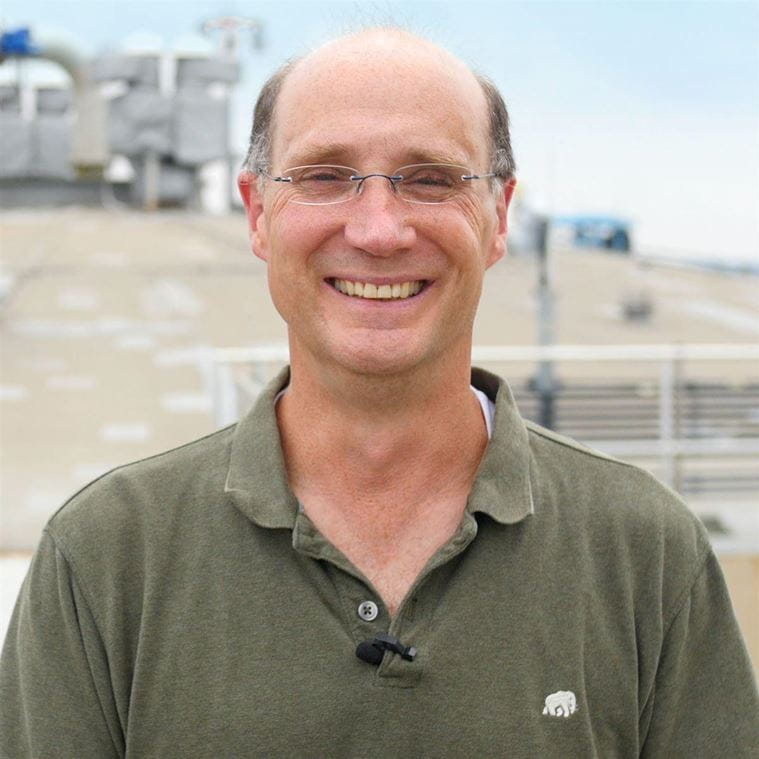
This project is the next generation of thermal hydrolysis, and it's been enhanced by our previous experience.
Net-Zero Means Better Choices
This project gives TRA many beneficial reuse options: creating a fertilizer product, composting or land application.