Best Practices: Using Membrane Bioreactors in Potable Reuse
Greg Wetterau, discipline leader for membrane technologies, and Anthony Zamarro, discipline leader for membrane bioreactors, deep dive into integrating MBRs for potable reuse, design and operating conditions, and other advanced treatment processes. Below is a recap from our latest webinar featuring Greg and Anthony.
Membrane bioreactors (MBRs) have been used since the early 2000s in North America as a reliable wastewater treatment process that combines the benefits of secondary clarification with a high-quality tertiary filter. More recently, MBRs have been considered for potable reuse schemes replacing both the conventional secondary clarifier and the tertiary ultrafiltration (UF) membrane system used as pretreatment for reverse osmosis (RO). When an MBR is implemented for potable reuse, special considerations for design and operation need to be addressed.
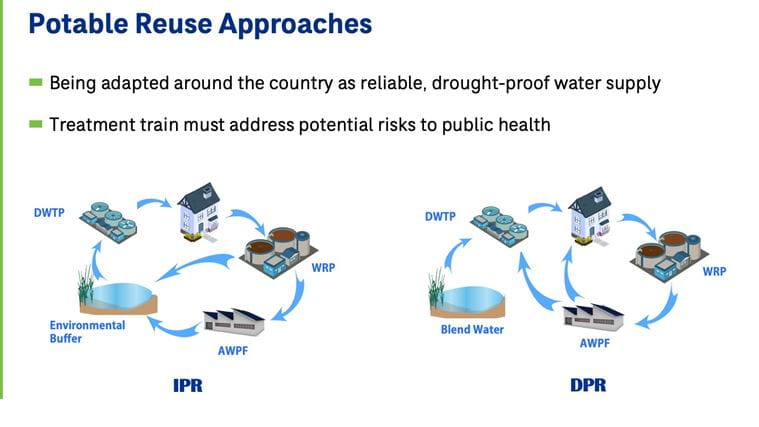
There are two main types of potable reuse: indirect potable reuse (IPR) and direct potable reuse (DPR). The key difference between these two methods is the use of an environmental buffer. IPR uses an environmental buffer, such as a lake, river, or a groundwater aquifer, before the water is treated at a drinking water treatment plant, to be sent back to the public. This treatment train is a complete loop, but the water spends part of the cycle within a natural environment, often receiving some degree of natural treatment. DPR involves the treatment and distribution of water without an environmental buffer. The water moves directly from the advanced water purification facility, either to a drinking water plant or directly to be used by the public. In DPR, some blending may occur from a natural water body, but the water within the reuse cycle does not pass through a natural environment.
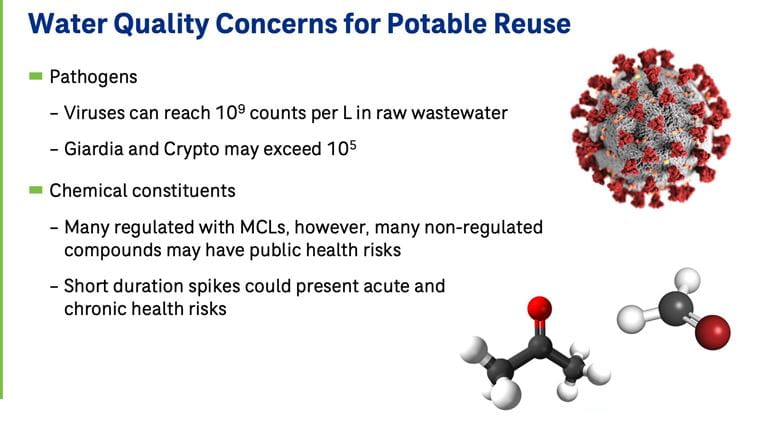
The level of treatment may differ from an IPR versus a DPR system, and the level of controls and safeguards may vary as well. There are two primary areas of risk for potable reuse: pathogen risks and chemical constituents. The initial source water for potable reuse is raw wastewater, where viruses can reach up to one billion (109) counts per liter, and Giardia and Cryptosporidium may reach one hundred thousand (105) organisms per liter. There must therefore be a higher level of treatment and control to address these potential pathogen levels.
The same is true for chemical constituents. Though maximum contaminant levels (MCLs) exist for many hazardous constituents, there are also a lot of non-regulated compounds that can pose public health risks and are often found at much higher levels than in natural water bodies. Short term spikes in hazardous chemicals may also occur in wastewater and would be returned to the drinking water if not adequately removed by the potable reuse system. At a potable reuse plant, monitoring must therefore be much more stringent, addressing this risk of short-term chemical spikes.
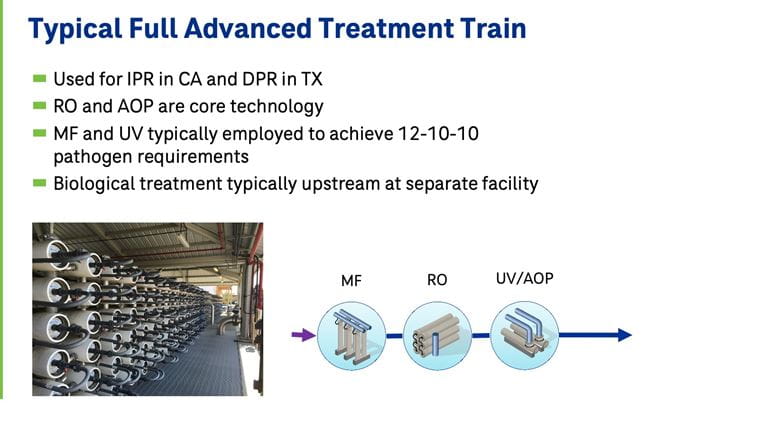
The core technology for full advanced treatment is reverse osmosis (RO) and advanced oxidation processes (AOP). In practice, all full advanced treatment plants also use either microfiltration (MF) or ultrafiltration (UF) as pretreatment for RO. Full advanced treatment plants also use ultraviolet (UV) light to generate their AOP. These core technologies are typically what experts refer to as full advanced treatment. All full advanced treatment plants currently include biological treatment upstream at a separate facility, so there is treatment occurring which may not be credited within the advanced treatment process.
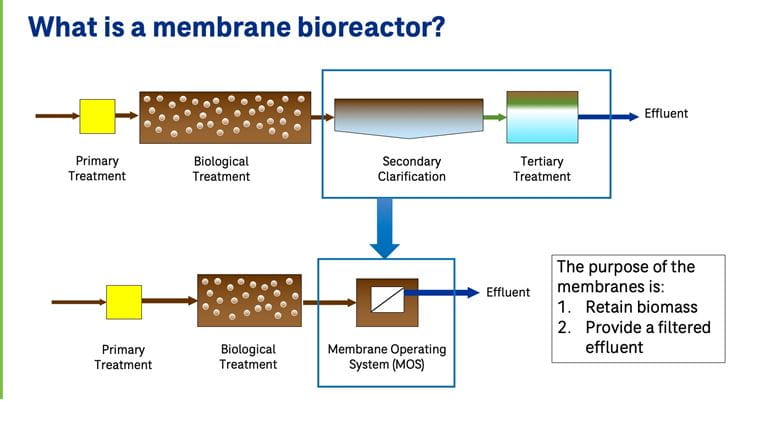
A membrane bioreactor (MBR) is a term used to define wastewater treatment processes where a semi-permeable membrane (like MF or UF) is integrated within a biological process. An MBR is essentially combining a secondary clarifier and any tertiary filters into one process using membranes. Membranes are positioned downstream of the biological process, and they serve as both the method for retaining biomass that gets recirculated back into the biological process, and a filtration step, producing a high-quality filtered effluent.
Two steps are compressed into one by using a membrane bioreactor. This treatment is more compact and efficient than a conventional process, and it allows for much higher solids concentrations to be maintained, increasing the removal efficiency for both dissolved and suspended contaminants. Running mixed liquor concentrations three to four times higher is a possibility using membrane bioreactors, unachievable at conventional plants. This provides more opportunity for compact facilities, while achieving a higher level of treatment.
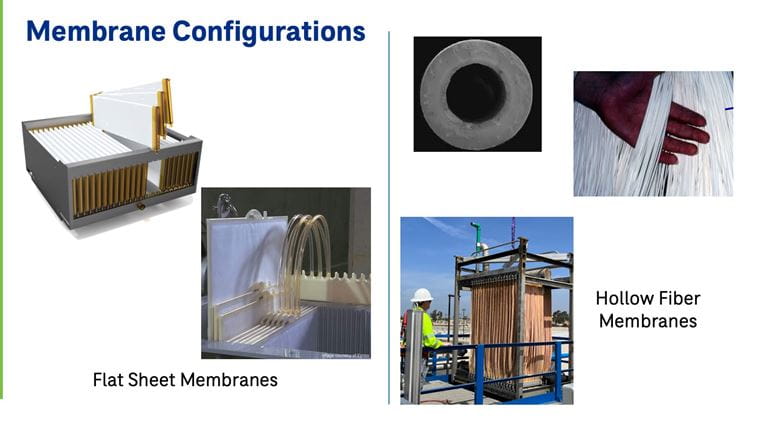
There are two types of membranes that are used at most MBRs: flat sheet and hollow fiber membranes. Flat sheets are more commonly used at smaller plants, and these may be polymeric or ceramic. A flat sheet membrane is essentially an envelope. Dirty water is on the outside, with clean water pulled into the center of the envelope through the membrane. Hollow fiber membranes function in a similar way but are configured more like straws. A large number of “straws” are bundled together in a module, then water is sucked through the walls of the straw via a vacuum, and clean water is released from the top.
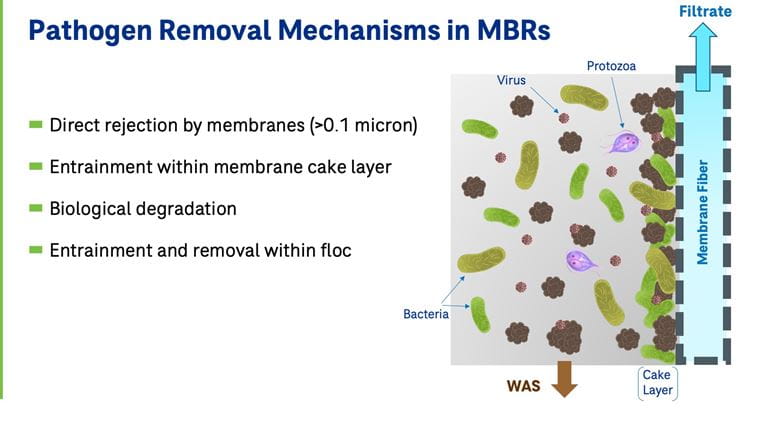
There are four different mechanisms for removal of pathogens in an MBR. The first one is direct rejection by the membranes. For example, if pores in a membrane are less than 0.1 micron, anything larger will be rejected, and anything smaller has the potential to come through.
As water moves into the membranes, it brings solids with it. The larger solids are rejected and build up on the surface of the membrane, forming a “cake layer” of dense solids. The cake layer is then able to remove some of the smaller materials that might otherwise pass through the membrane pores. A virus that is small enough to pass through the pores may still be entrained on the cake layer, so it is removed by the process.
Additionally, biological degradation is occurring. “Bugs”—or bacteria that metabolize organic compounds in raw water—are eating other bugs. The wastewater process is set up with separate anoxic and aerobic zones so there are different dominant bugs in each of the tanks. As solids cycle through, pathogens are being broken down, with the remaining microbes primarily the non-pathogenic type.
The last method is entrainment and removal with the floc. As solids are recirculated, waste activated sludge, is removed from the system. Pathogens which have become attached to the wasted floc will be removed with these solids.
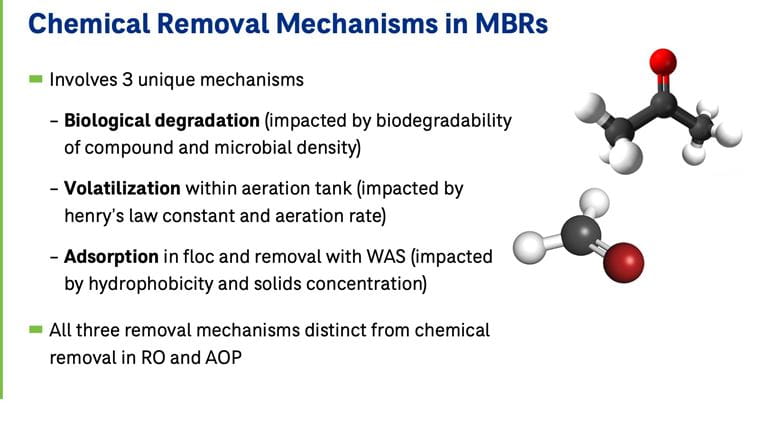
There are three different mechanisms involved with the removal of chemicals in an MBR. The first is biological degradation. In this process, bugs consume the biodegradable chemicals, using them as a carbon source, and converting them to carbon dioxide, methane, or other organic compounds. The ability to remove chemicals through this method not only depends on the biodegradability, but also on microbial density. In an MBR, there is a much higher microbial density because mixed liquor concentrations are much higher than at a conventional wastewater plant. More biology exists in an MBR, resulting in greater opportunity to biologically degrade these compounds.
The second removal mechanism is volatilization. Air is bubbling within the aeration tank, so volatile compounds with a higher henry's law constant are more likely to be removed. If aeration rates are higher, there will be more volatilization, and MBRs tend to have more aeration than a conventional plant- not just in the main aerobic tank, but also within the MBR tank. With the higher aeration rates, there is potential for more removal of volatile compounds.
The last removal mechanism is adsorption. The possibility exists to adsorb these chemicals into the floc, and when the waste activated sludge is sent out, the chemicals will be removed that way. This removal is impacted by higher hydrophobicity. More hydrophobic components are more likely to adsorb on the floc. If there are higher solid concentrations- similar to MBR processes- then there is greater potential for adsorption as well.
All three of these removal types are enhanced at an MBR compared to a conventional plant. It’s important to note that these removal mechanisms are all unique compared to the removal at a full advanced treatment plant.
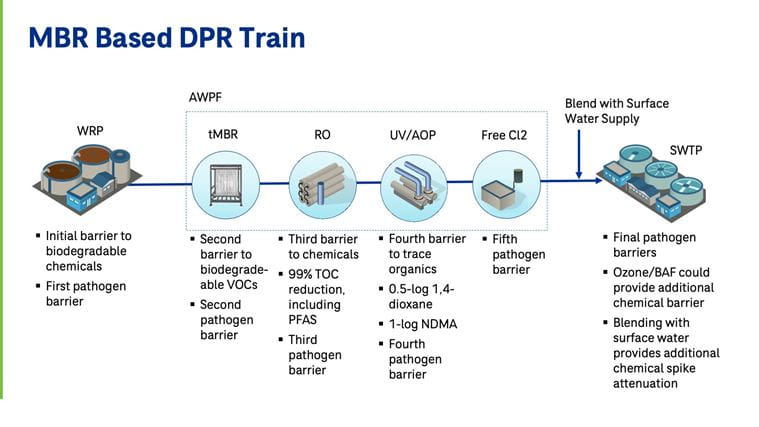
There are a few ways to integrate an MBR into a potable reuse train. Incorporating an MBR downstream of a water reclamation plant is one option- this is considered a tertiary MBR. It becomes a second barrier for biodegradable organics and a second pathogen barrier. There is an additional option to combine the MBR with a water reclamation plant as a more traditional, secondary MBR. The MBR offers a controlled step for removal of biodegradable components, as well as a pathogen barrier, ahead of the downstream processes already included in full advanced treatment. Several facilities in California are examining treatment trains like this for potable reuse, and their consideration is expected to rise as potable reuse becomes more prevalent throughout the country.
Anthony Zamarro has worked in membrane technologies and treatment systems for more than 20 years with a focus on membrane bioreactor (MBR) systems. He has experience in system design, value engineering, system startup, and process troubleshooting. He has also been involved in the application of MBR systems for advanced treatment trains, including indirect and direct potable reuse (IPR/DPR) applications.
Greg Wetterau is a senior environmental engineer who has been involved in the piloting, design and facility start-up for more than 60 membrane treatment facilities around the world, with over two decades of experience at the firm. His expertise in process and system design for desalination and advanced wastewater treatment has helped clients like the Water Replenishment District of Southern California expand and upgrade their potable reuse facility, all while complying with evolving state regulations.
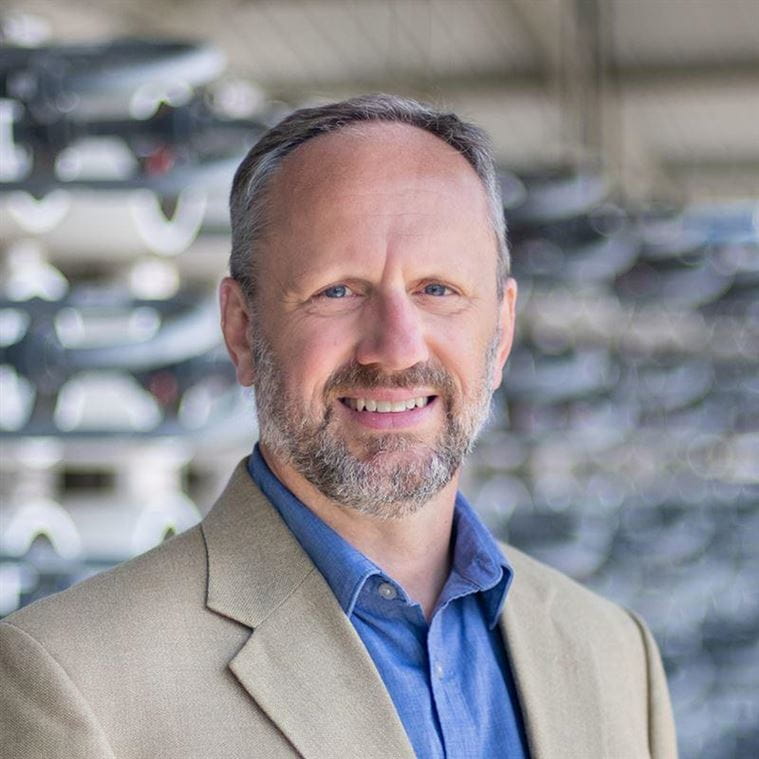
By gathering enough information and being creative, we can develop the right treatment approach for each situation.
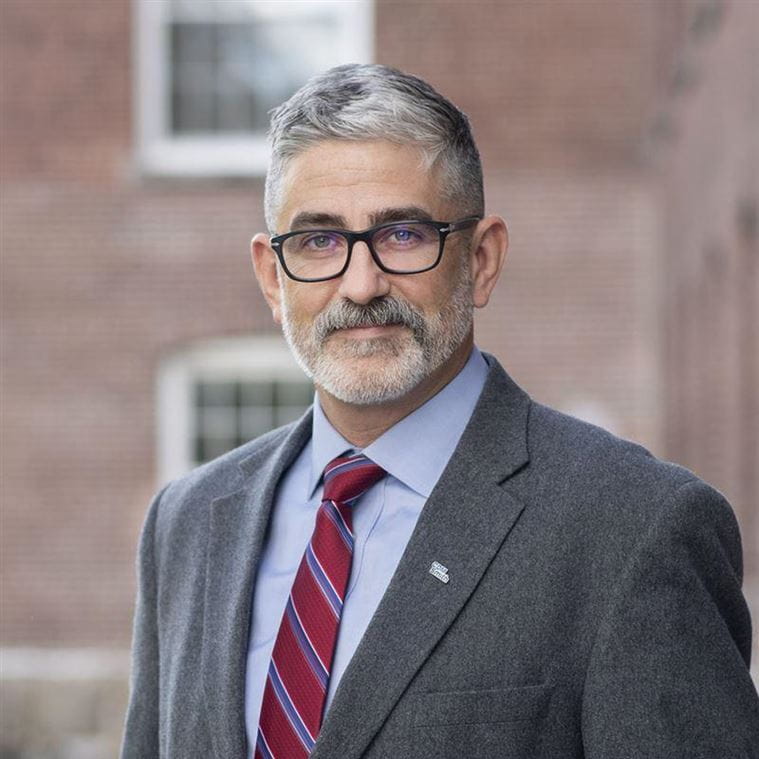
We've come a long way with MBRs and they are moving into a new operational window.
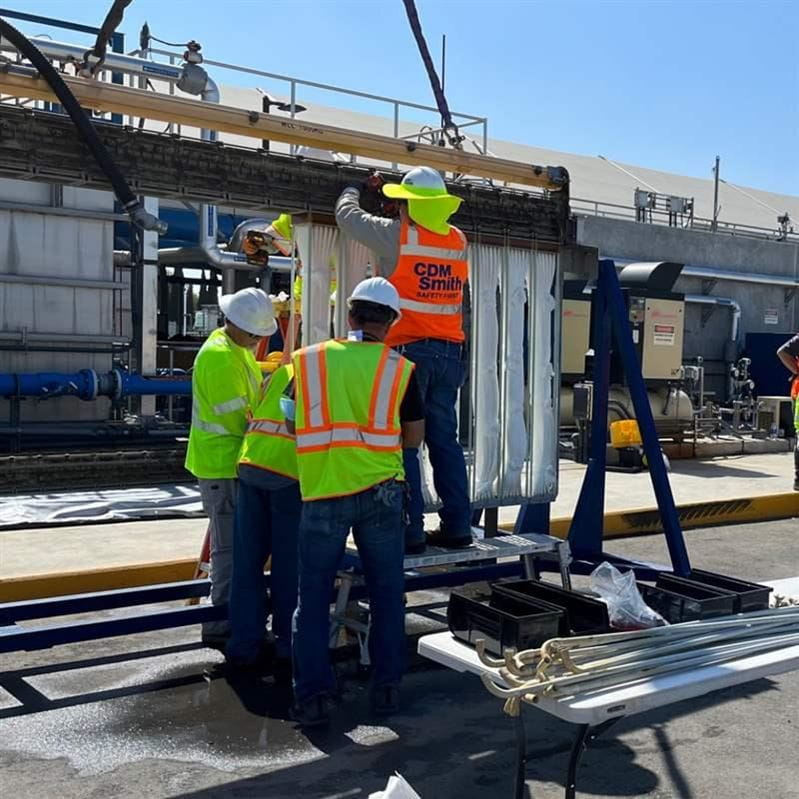
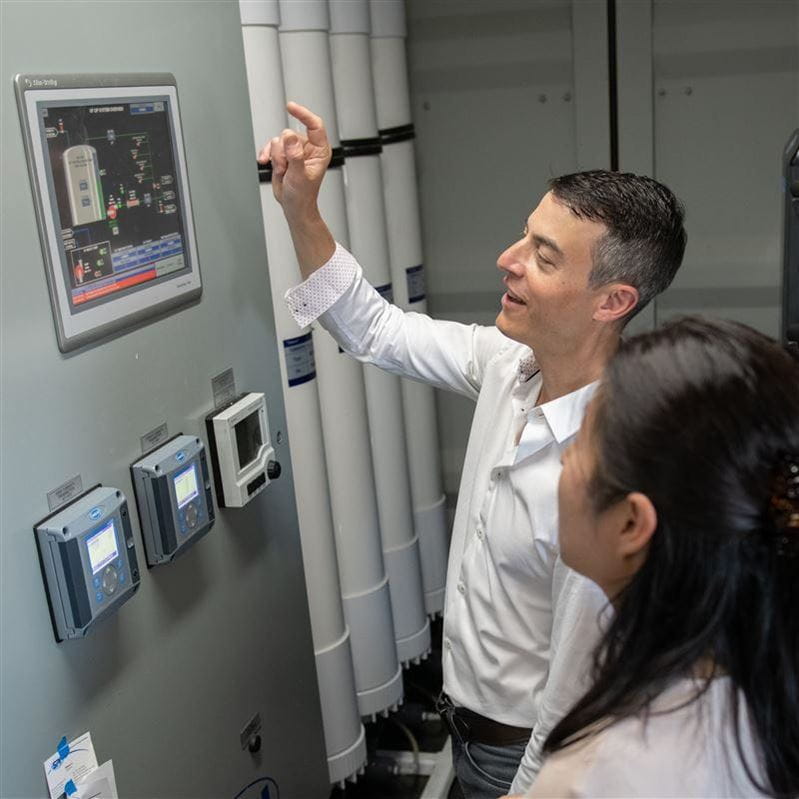