Mission Ready at Training Center Cape May
To support their enduring mission, the Coast Guard commissioned the advanced $11.4 million station at Training Center (TRACEN) Cape May in New Jersey. Designed and constructed by CDM Smith, the new station better serves the Coast Guard’s operational needs in the Delaware Bay and mid-Atlantic region. The nation's only Coast Guard recruit training center, Cape May is also home to three 87-foot search-and-rescue cutters and Aids to Navigation Team (ANT), which oversees the region’s navigation aids and lighthouses.
Previously, the station and ANT operated from a World War II-era laundry facility and a scattering of undersized and temporary structures. Bringing them together is a state-of-the-art, two- story 29,900-square-foot (sf) multi-mission building that comfortably houses 80 personnel and their equipment. The building provides administrative and operational control space, large training rooms with advanced audio/visual systems, wet rooms, an armory and telecommunications command center, two large boat bays with engineering spaces, and comfortable berthing for the station watch standers and temporarily assigned personnel.
The adjacent new one-story, 6,800-sf vessel support facility includes three open work bays for smaller, towable boats and secure storage for naval engineering supplies, all designed to give staff efficient and effective maintenance space. To support the Coast Guard’s environmental commitment, the LEED®-certified buildings feature local and recycled products, surpass indoor air quality standards, incorporate water-saving landscape design and interior fixtures, and use energy- efficient lighting. Midway through the design, the project team was asked to accommodate the Vessel Boarding Security Team, a homeland security unit that relocated from Philadelphia, Pennsylvania.
Previously, the station and Aids to Navigation Team operated from a World War II-era laundry facility and a scattering of undersized and temporary structures.
Keeping the 24-month project on schedule required flexible and innovative planning on the busy base. The two new buildings were to be built on adjacent sites separated by an active roadway. Operations were to continue in the existing structures and then move to the completed multi-mission building, making room for the new vessel support facility. A unique site design allowed the simultaneous construction of both buildings by incorporating the existing roadway and footprints into a unified site. The use of pre-engineered metal buildings further reduced project costs and time, and the ocean-side base also required structural and geotechnical engineers to develop appropriate pile, foundation and slab designs, which allowed construction to progress while other teams completed their designs.
Today, TRACEN truly has a 21st century facility that supports the U.S. Coast Guard's objectives to modernize its facilities and fleet and be as green as possible.
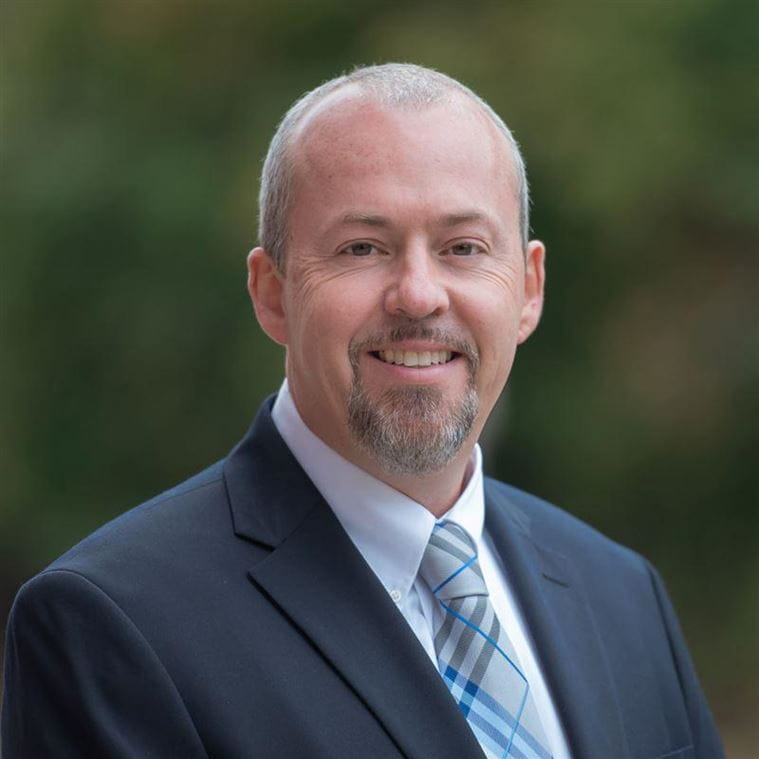
Training Center Cape May is a 21st century facility that supports the Coast Guard's objectives to modernize its facilities and fleet and to be as green as possible.
Training Center Cape May features LEED®-certified buildings.